
Diagnostics Services on Gearboxes and General Rotating Equipment
Examples of Machine Diagnostics possibilities - 8 different types of projects
Our VIBXPERT is a high performance, full-featured 2 channel FFT data collector and signal analyzer. This instrument is most frequently used by our engineers on medium and low speed machinery running on rolling element bearings, such as found in the petrochemical, pulp and paper industries.
This VIBXPERT 2-channel data collector is particularly well suited for:
- Identification of rolling element bearing problems
- Identification of gear related defects
- Looseness problems
- Periodic condition monitoring of large numbers of machinery
- Simple in-situ single plane balance jobs
- Analyzing vibration problems in harsh environments, such as wind turbines and harbour cranes.
This VIBXPERT 2-channel data collector is particularly well suited for:
- Identification of rolling element bearing problems
- Identification of gear related defects
- Looseness problems
- Periodic condition monitoring of large numbers of machinery
- Simple in-situ single plane balance jobs
- Analyzing vibration problems in harsh environments, such as wind turbines and harbour cranes.
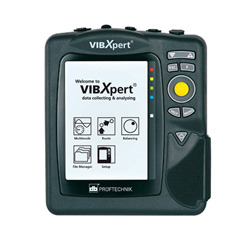
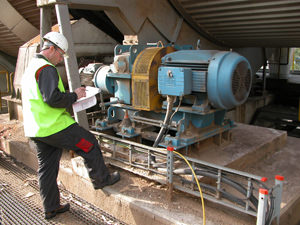
Rolling element bearing damage - Example project No.1
More and more customers are changing from scheduled maintenance towards a condition based maintenance program. Predicting or monitoring the condition of machinery becomes therefore very important.
What GBS Gearbox Services international offered:
Hundreds of job are performed by our engineers to predict the condition of all sorts of gearboxes, such as wind turbine gearboxes, crane hoisting gearboxes, extruder gearboxes, etc. With the use of our instruments and our extensive experience we are able to predict the condition of the gearbox with maximum reliability.
The following techniques are used (often in combination):
- Visual inspection (if necessary with the help of our videoscope)
- Vibration measurements
- Oil sampling and analyzing
A rolling element bearing inner ring defect was identified in the plot below.
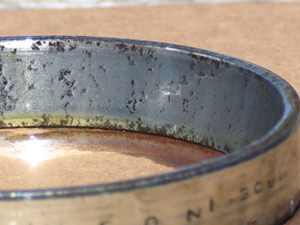
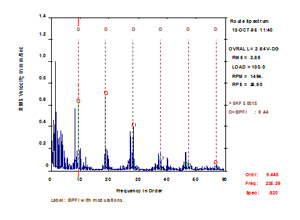
What GBS Gearbox Services international offered:
Hundreds of job are performed by our engineers to predict the condition of all sorts of gearboxes, such as wind turbine gearboxes, crane hoisting gearboxes, extruder gearboxes, etc. With the use of our instruments and our extensive experience we are able to predict the condition of the gearbox with maximum reliability.
The following techniques are used (often in combination):
- Visual inspection (if necessary with the help of our videoscope)
- Vibration measurements
- Oil sampling and analyzing
A rolling element bearing inner ring defect was identified in the plot below.
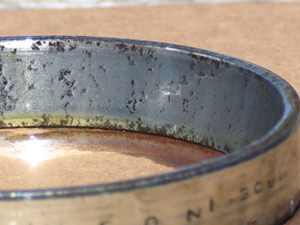
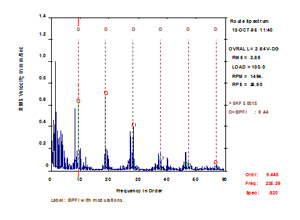
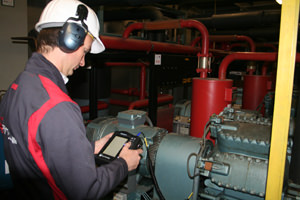
Identification and elimination of a clearly noticeable impact - Example project No.2
Overloading or other process related incidents could create local damage to the gears. In some occasions this damage will create noticeable impacts during operation of the gearbox.
What GBS Gearbox Services international offered:
To identify the specific gear and even the specific tooth causing the impact we used our portable data acquisition system in combination with an acceleration sensor and a keyphasor. The plot below shows the result when collecting the data. The dotted line represents the passing keyphasor (trigger) mark, while the impact is shown by a spike in the signal. Calculation of the exact position of the impact is now possible.
Sometimes hand grinding is enough to remove the burrs caused by an indentation. In other occasions it was necessary to re-grind the gears by a specific gear grinding machine.
What GBS Gearbox Services international offered:
To identify the specific gear and even the specific tooth causing the impact we used our portable data acquisition system in combination with an acceleration sensor and a keyphasor. The plot below shows the result when collecting the data. The dotted line represents the passing keyphasor (trigger) mark, while the impact is shown by a spike in the signal. Calculation of the exact position of the impact is now possible.
Sometimes hand grinding is enough to remove the burrs caused by an indentation. In other occasions it was necessary to re-grind the gears by a specific gear grinding machine.
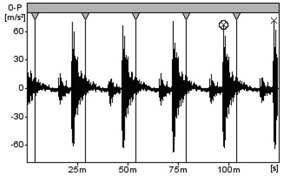
Identification of gear related problems - Example project No.3
Gear damage is often a secondary effect of another problem, such as overloading, misalignment between the gears, degraded lubrication oil properties, ect. The progression of gear damage, such as micro pitting could be stopped if the root cause of the problem is found and corrected in time.
What GBS Gearbox Services international offered:
By recording the gearbox casing vibrations we were able to identify the particular gear that was causing the increased vibration level. In this case the damage was too severe and the gear had to be re-placed. In other cases however with minor damage it might be sufficient to replace the bearings when excessive bearing clearance is the root cause.
What GBS Gearbox Services international offered:
By recording the gearbox casing vibrations we were able to identify the particular gear that was causing the increased vibration level. In this case the damage was too severe and the gear had to be re-placed. In other cases however with minor damage it might be sufficient to replace the bearings when excessive bearing clearance is the root cause.
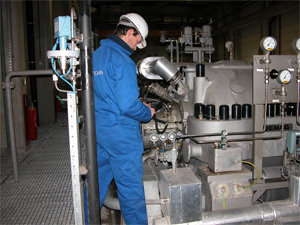
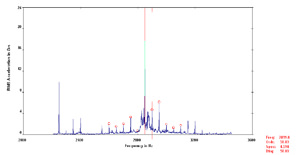
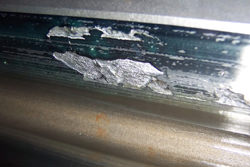
Multichannel data acquisition system from Bently Nevada - Example project No.4
Overloading or other process related incidents could create local damage to the gears. In some occasions this damage will create noticeable impacts during operation of the gearbox.
What GBS Gearbox Services international offered:
To identify the specific gear and even the specific tooth causing the impact we used our portable data acquisition system in combination with an acceleration sensor and a keyphasor. The plot below shows the result when collecting the data. The dotted line represents the passing keyphasor (trigger) mark, while the impact is shown by a spike in the signal. Calculation of the exact position of the impact is now possible.
Sometimes hand grinding is enough to remove the burrs caused by an indentation. In other occasions it was necessary to re-grind the gears by a specific gear grinding machine.
What GBS Gearbox Services international offered:
To identify the specific gear and even the specific tooth causing the impact we used our portable data acquisition system in combination with an acceleration sensor and a keyphasor. The plot below shows the result when collecting the data. The dotted line represents the passing keyphasor (trigger) mark, while the impact is shown by a spike in the signal. Calculation of the exact position of the impact is now possible.
Sometimes hand grinding is enough to remove the burrs caused by an indentation. In other occasions it was necessary to re-grind the gears by a specific gear grinding machine.
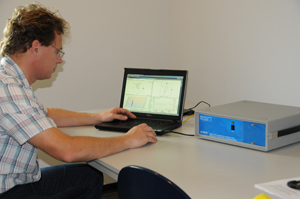
Delaval barrel type Gas Compressor with high shaft vibrations - Example project No.5
A customer noticed a sudden increase of the shaft vibration level on their Bently Nevada vibration protection system. The customer contacted us to identify the root cause of the problem and if the problem could be solved without major down time.
What GBS Gearbox Services international offered:
Our ADRE system was connected to the customers protection system for advanced diagnostic capabilities under different operational conditions. The recorded data had all the characteristics of unbalance. The vibration level was related to speed. The frequency was equal to the rotational frequency of the compressor and the orbit figures were circular on both ends of the rotor. It was decided not to balance the rotor in-situ due to the fact that the increase of vibration level happened suddenly, which suggests that something is stuck inside the rotor, broken of or shifted.
During dismantling of the compressor it became clear that a piece of strainer had entered the compressor and got stuck within one of the impellers.
What GBS Gearbox Services international offered:
Our ADRE system was connected to the customers protection system for advanced diagnostic capabilities under different operational conditions. The recorded data had all the characteristics of unbalance. The vibration level was related to speed. The frequency was equal to the rotational frequency of the compressor and the orbit figures were circular on both ends of the rotor. It was decided not to balance the rotor in-situ due to the fact that the increase of vibration level happened suddenly, which suggests that something is stuck inside the rotor, broken of or shifted.
During dismantling of the compressor it became clear that a piece of strainer had entered the compressor and got stuck within one of the impellers.
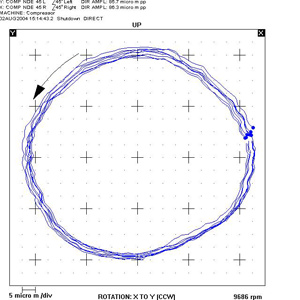
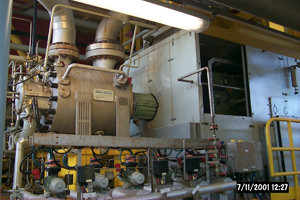
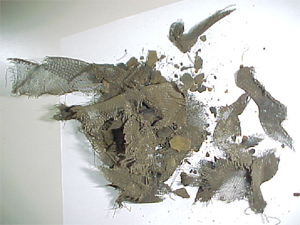
Luxury yacht with excessive hull vibrations - Example project No.6
A specific type of yacht had vibration problems which occured at a certain sailing speed. The cause of this vibration is currently under investigation by the ship builder. As a possible cause, the propeller shafts were pointed out. Excessive shaft vibration is thought to excite a hull resonance.
What GBS Gearbox Services international offered:
By measuring the displacement of the propeller shaft, we answered the question whether the propeller shaft is causing the vibration problem and under which circumstances it occurs.
What GBS Gearbox Services international offered:
By measuring the displacement of the propeller shaft, we answered the question whether the propeller shaft is causing the vibration problem and under which circumstances it occurs.
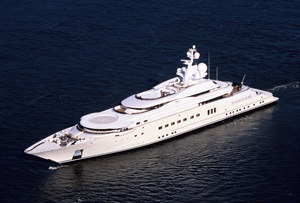
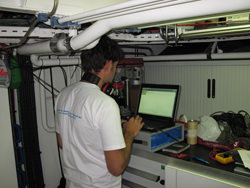
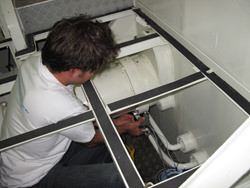
Commissioning / acceptance surveys - Example project No.7
Our engineers assisted many customers around the world during commissioning of their newly installed or overhauled installations.
What GBS Gearbox Services international offered:
During commissioning we were able to verify if the recorded dynamic behaviour of the machine was conform international recognized standards, such as API or ISO. ADRE was used for data acquisition and is normally connected to the customers vibration protection system. Acceptance reports are made including all relevant machine baseline information. In other occasions the recorded data was used to discuss corrective actions. We also assisted customers with programming and optimizing their online condition monitoring systems.
What GBS Gearbox Services international offered:
During commissioning we were able to verify if the recorded dynamic behaviour of the machine was conform international recognized standards, such as API or ISO. ADRE was used for data acquisition and is normally connected to the customers vibration protection system. Acceptance reports are made including all relevant machine baseline information. In other occasions the recorded data was used to discuss corrective actions. We also assisted customers with programming and optimizing their online condition monitoring systems.
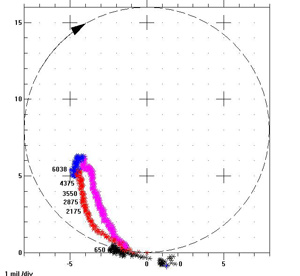
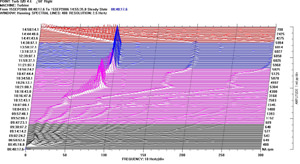

Gas turbine balancing, GE Frame 5 (MS 5001) - Example project No.8
A customer was operating their compressor close to the vibration alarm setpoint. Our engineers were asked to analyze the problem and if possible reduce the vibration level.
What GBS Gearbox Services international offered:
Transient vibration data was recorded with our ADRE system to identify the root cause of the elevated vibration levels. In this case unbalance caused by fouling on the impellers was identified as the root cause. After repeatability of the problem was confirmed and rotor washing did not show any influence it was decided to balance the machine in situ. In situ trim balancing is a very cost effective way to reduce elevated vibration level without taking the machine apart.
Reference list of balance jobs all executed with ADRE equipment:
- GE Frame 5 (MS 5001) gas turbines
- GE Frame 6B gas turbines
- GE Frame 9FA gas turbines
- GE LM 1600 power turbines
- GE LM 2500 gas turbines
- GE LM 6000 gas turbines
- Siemens V64 gas turbines
- Siemens Tornado power turbines
- GE Steam Turbines
- Solar barrel compressors
- Delaval (Siemens) barrel compressors
- Nuovo Pignone barrel compressors
- Elliott horizontal split line compressors
- Kawasaki centrifugal air compressor
- Praxair cryogenic expander
- Flow serve boiler feed water pump
- A large number of ventilators
What GBS Gearbox Services international offered:
Transient vibration data was recorded with our ADRE system to identify the root cause of the elevated vibration levels. In this case unbalance caused by fouling on the impellers was identified as the root cause. After repeatability of the problem was confirmed and rotor washing did not show any influence it was decided to balance the machine in situ. In situ trim balancing is a very cost effective way to reduce elevated vibration level without taking the machine apart.
Reference list of balance jobs all executed with ADRE equipment:
- GE Frame 5 (MS 5001) gas turbines
- GE Frame 6B gas turbines
- GE Frame 9FA gas turbines
- GE LM 1600 power turbines
- GE LM 2500 gas turbines
- GE LM 6000 gas turbines
- Siemens V64 gas turbines
- Siemens Tornado power turbines
- GE Steam Turbines
- Solar barrel compressors
- Delaval (Siemens) barrel compressors
- Nuovo Pignone barrel compressors
- Elliott horizontal split line compressors
- Kawasaki centrifugal air compressor
- Praxair cryogenic expander
- Flow serve boiler feed water pump
- A large number of ventilators
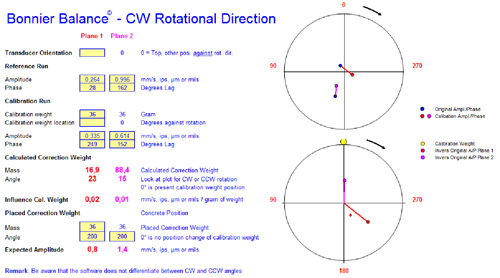