
Inspection, on-site or in our shop
Gearbox Inspection
Our Engineering staff, Technical Sales Personnel and Field Service Technicians understand the critical demands placed on specific field applications of gear drive systems. Based on our combined experience of more than 20 years, we are able to execute complete inspections of gearboxes. Our inspections can include:
- Visual inspection
- Videoscope inspection
- Contact pattern checking
- Check dimensions and tolerances
- Damage cause analysis
- Strength calculations
- Control alignment
- Vibration analysis
Inspections can be executed in our factory and on customers location, as well running as not running.
- Videoscope inspection
- Contact pattern checking
- Check dimensions and tolerances
- Damage cause analysis
- Strength calculations
- Control alignment
- Vibration analysis
Inspections can be executed in our factory and on customers location, as well running as not running.
After every inspection we offer You an clear inspection report, based on facts, with conclusions and advises.
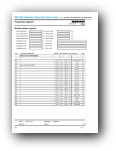
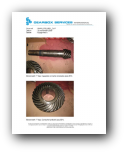
1. Visual inspection
If the gearbox must be dismantled, since severe damage is present, the entire gearbox will be thoroughly visually inspected. We also conduct a NDO study on the gears.
If the gearbox must be dismantled, since severe damage is present, the entire gearbox will be thoroughly visually inspected. We also conduct a NDO study on the gears.
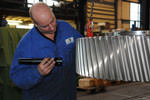
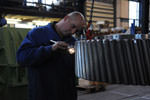
2. Videoscope inspections
To prevent a dismantling of the gearbox, we can perform an inspection by video scopy.
To inspect rolling element bearings and gears, we use the latest videoscopes from General Electric. These videoscopes allow us to identify problems, often impossible to see by the naked eye.
To prevent a dismantling of the gearbox, we can perform an inspection by video scopy.
To inspect rolling element bearings and gears, we use the latest videoscopes from General Electric. These videoscopes allow us to identify problems, often impossible to see by the naked eye.
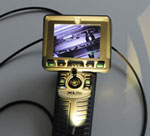
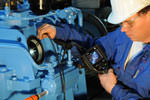
3. Contact patern checking
Before dismantling the gearbox we check al the contact paterns.
Before dismantling the gearbox we check al the contact paterns.
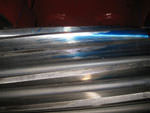
4. Check dimensions and tolerances
When decided that the gearbox should be overhauled, all dimensions of all parts are checked and judged with our latest experience and engineering rules.
When decided that the gearbox should be overhauled, all dimensions of all parts are checked and judged with our latest experience and engineering rules.
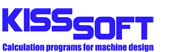
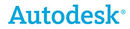
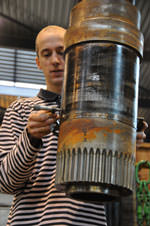
5. Damage cause analyses / Strenght calculations
We allways want to know the cause of damage. If this is not clear, we will recalculate the gearbox on strength. We therefore have for example the well known software "KissSoft". It's allways necessary for us to understand the reason for collapsing, because we are offering You 6 months guarantee.
We allways want to know the cause of damage. If this is not clear, we will recalculate the gearbox on strength. We therefore have for example the well known software "KissSoft". It's allways necessary for us to understand the reason for collapsing, because we are offering You 6 months guarantee.
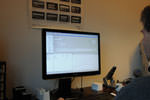
6. Alignment checking
Second to rotor unbalance, misalignment is a frequently encountered problem. GBS is able to handle both hot and cold alignment projects on your machinery as well as reciprocating compressors in addition to rotating machinery. Our services are available from simple two case machine configurations to more complex multi-case situations such as large steam turbine generators.
Second to rotor unbalance, misalignment is a frequently encountered problem. GBS is able to handle both hot and cold alignment projects on your machinery as well as reciprocating compressors in addition to rotating machinery. Our services are available from simple two case machine configurations to more complex multi-case situations such as large steam turbine generators.
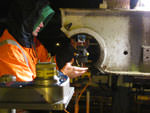
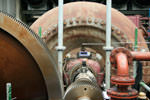
7. On-site troubleshooting
Our knowledge, experience and equipment allows us to identify potential machinery malfunctions, such as rolling element bearing defects, gear related problems, rubs, resonances, etc. Significant and valuable time can therefore be saved to resolve the problem.
Our knowledge, experience and equipment allows us to identify potential machinery malfunctions, such as rolling element bearing defects, gear related problems, rubs, resonances, etc. Significant and valuable time can therefore be saved to resolve the problem.
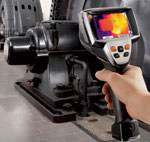
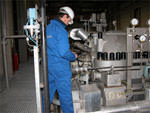